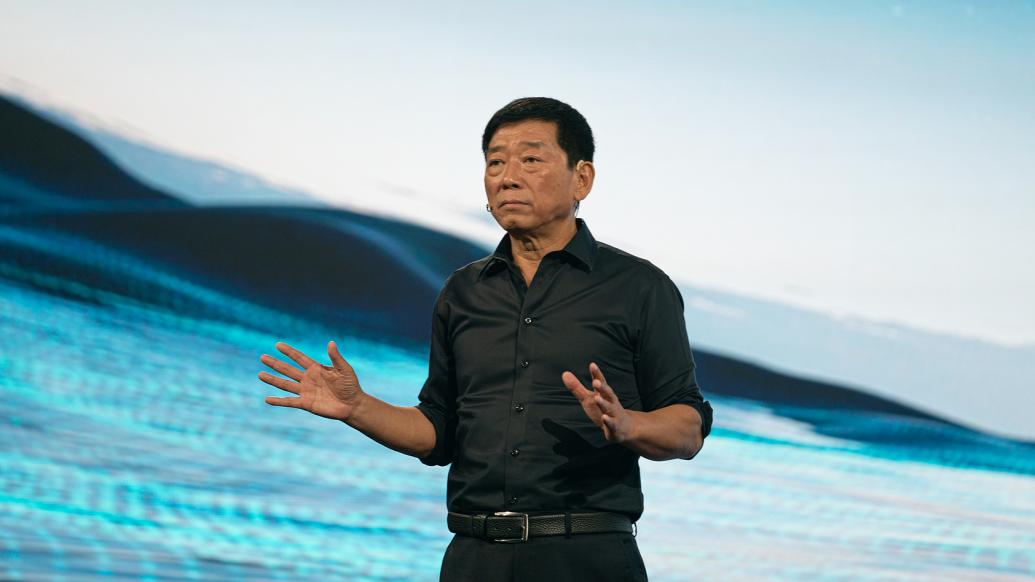
Recently, during a media interview, Great Wall Motors Chairman Wei Jianjun made a controversial statement: “Chinese electric vehicles lack core technology; we only have a leading industrial chain,” sparking renewed debate.
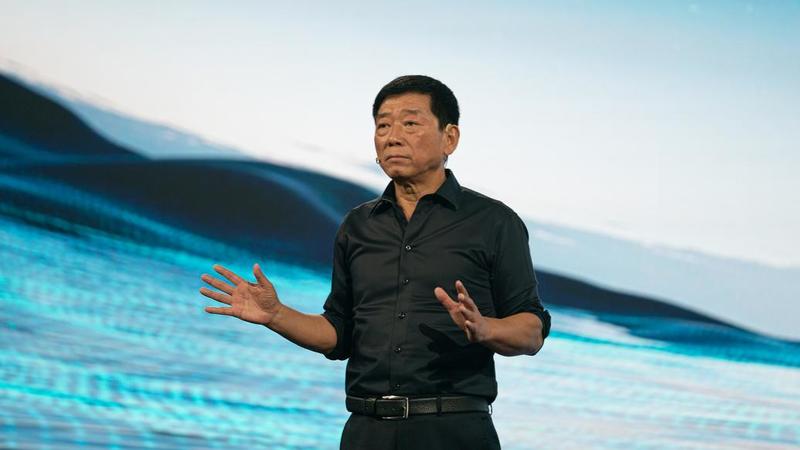
Great Wall Motors Chairman Wei Jianjun
To avoid misinterpretation, his full view is as follows: “In terms of traditional internal combustion engine technology, we certainly lag behind foreign brands; when it comes to electric vehicles, those companies have technology but lack this strategy. Our Chinese power batteries originated from the United States, traced back to Japan, and have been further developed by South Korea. However, the industrial chain for electric vehicles in China is unparalleled; this is the only area where we lead. As for components like motors and electronic controls, the chips we use are American, but we excel in our algorithms, which is something we should encourage.”
In fact, while Wei Jianjun's viewpoint may be unsettling, it does not stray from the truth.
In the era of fuel vehicles, the three key components—engine, transmission, and chassis—saw mainstream automakers forming alliances with upstream suppliers to craft their unique recipes, thereby securing their position within the supply chain and enhancing their industry influence. A typical example is Toyota and its key suppliers: Denso, Toyota Tsusho, Tokai Rika, Aisin Seiki, among others. Similarly, BMW with ZF, and General Motors with Delphi (now Aptiv) also illustrate strong partnerships. Once these barriers are established, it becomes difficult for newcomers to enter the system, contributing to why Chinese automakers struggle to surpass their overseas counterparts in fuel vehicle technology.
Now, in the age of electric vehicles, the “three key components” have transformed into batteries, motors, and electronic controls, with an added emphasis on intelligence. In terms of batteries, CATL and BYD lead the market; for motors, companies like Weichai Power and Hunan Intellifusion rank at the top. However, in the realm of smart technology, despite the diversity and complexity of applications available in Chinese electric vehicles, a closer look reveals that the fundamental chips are often products from overseas companies such as NVIDIA, Intel, and Qualcomm.
Therefore, the leadership in electric vehicles is, in fact, more about certain excellent suppliers leading the way, rather than a comprehensive lead by Chinese automakers. Aside from BYD, which boasts a nearly closed-loop vertical industrial chain, no other Chinese automotive companies currently possess this capability.
From this perspective, Wei Jianjun's assertion that “we only lead in the industrial chain” holds some truth.
However, expanding the discussion, if so-called “technological leadership” remains confined to laboratories without the support of an industrial chain to accelerate its adoption, then it ultimately loses significance. Thus, the relationship between leading the industrial chain and technological leadership is not one of separation, but rather one of mutual support.
For instance, in 2016, the Tesla Model 3 employed 48 silicon carbide power chips from STMicroelectronics, drastically reducing the size and weight of the inverter and improving efficiency by 8%, enhancing the vehicle's range by 10%. Subsequently, Tesla's hot sales propelled the previously obscure Wolfspeed company to become a dominant player in global silicon carbide substrates, prompting major automakers to follow suit, leading to a supply-demand imbalance that drove up silicon carbide costs. Yet, Tesla hesitated to shift to the 800V high-voltage route.
Wolfspeed subsequently faced declining order volume from Tesla, resulting in reduced capacity utilization, consecutive losses, and a stock price plummeting from a peak of $140 to $7. As the sole player in the U.S. silicon carbide substrate market, the company eventually received $750 million in subsidies from the U.S. Department of Commerce. To this day, the company is on the brink of disaster, losing $600 million each quarter. This scenario exemplifies how an immature industrial chain can hinder technological dissemination.
In contrast, the situation in China is quite different. Supported by a robust industrial chain, many automakers adopt a “buffet-style” approach to vehicle manufacturing. It can be said that in China, building electric vehicles is less about branding; they essentially serve as “technology carriers” for excellent suppliers.
Thus, in a heartbeat, when firms like WM Motor and Aiways fall, new players like Xiaomi and AITO can emerge. As automakers rise and fall, the rotation of brands does not disrupt the continuous advancement of technology and the enhancement of user experience.
From this standpoint, while we need to catch up in core technology, the advantage of leading the industrial chain is equally important and should not be underestimated.