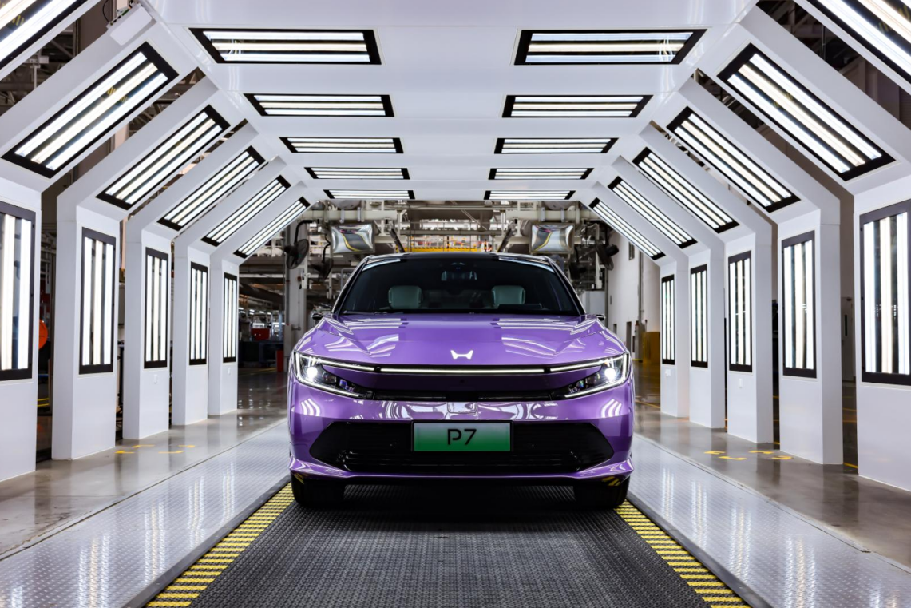
On March 26, the inauguration ceremony of GAC Honda's new energy factory in the Development Zone and the roll-out ceremony of the new electric vehicle P7 were officially held.
This day has a special meaning for GAC Honda - on March 26, 1999, the first domestically produced Accord rolled off the production line at its Huangpu factory, establishing GAC Honda's leading position in the domestic mid-to-high-end sedan market; on the same day 26 years later, the P7 electric car, which represents GAC Honda's determination to develop in the new energy era, rolled off the production line.
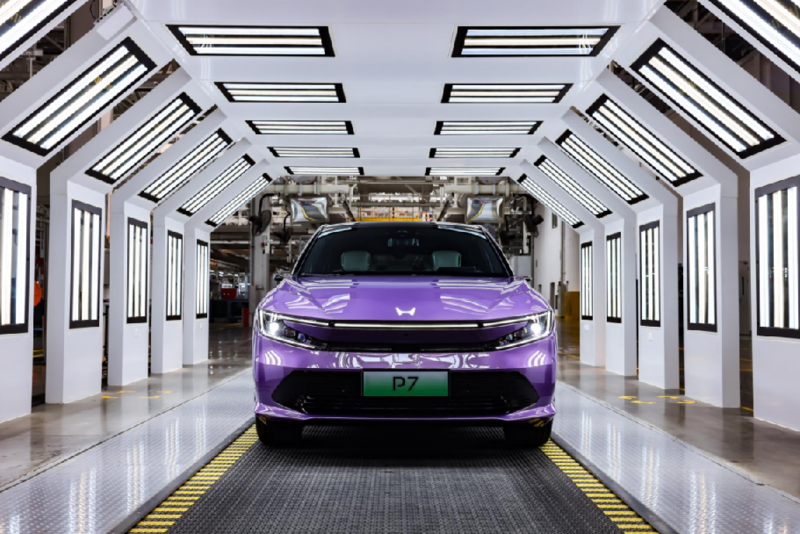
The GAC Honda P7 not only inherits Honda's consistent driving pleasure gene, but also has been further upgraded in terms of durability and quality. It is reported that the P7 body adopts all-round aluminum-zinc coating for corrosion and rust prevention, and is equipped with a high-resistance, long-lasting and transparent 2K varnish process. Compared with the traditional 1K varnish, the paint film thickness is increased by 50%, the paint surface smoothness is increased by 57.8%, the leveling is better, the acid resistance is increased by 97%, and the scratch resistance is increased by 28%.
The ability to achieve such extreme craftsmanship is thanks to the factory where the P7 is located. With a total investment of 3.5 billion yuan and an annual production capacity of 120,000 vehicles, this new energy factory integrates more than 30 global leading technologies, more than 50 domestic leading technologies, and nearly 60 technologies that Honda has applied for the first time in the world.
At the digital level, the GAC Honda Development Zone New Energy Factory has achieved full-link data connectivity and intelligent, efficient and flexible production through the deep integration of digitalization and intelligent technology: 100% data connection between the MES system and the equipment monitoring system is used to improve the response speed of the linkage between production planning and performance; the stamping workshop adopts a full servo production line, which can produce one/a pair of stamping parts in as fast as 3.75 seconds. After the parts are produced, they are 100% automatically packed by robots; the welding workshop achieves 100% automation of welding, and applies the industry's first welding AI detection to ensure that the body welds are 100% qualified.
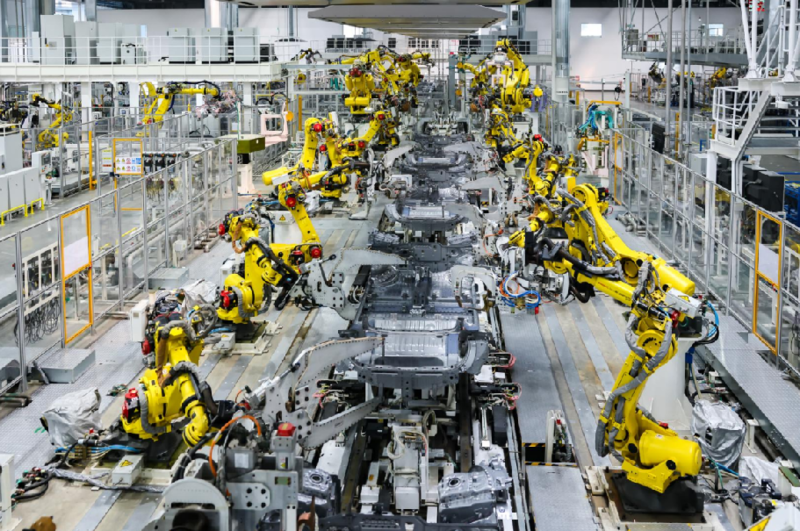
The paint shop uses the industry's advanced dosing machines and spray gun systems to achieve 100% automatic gluing of the entire vehicle. Combined with the visual positioning system, the gluing accuracy reaches 0.5mm; the overall automation rate of the assembly workshop is nearly 3 times the level of the domestic automobile industry, and the introduction of automatic parts delivery AGV and direct supply conveyor lines has achieved a 25% increase in logistics efficiency.
In terms of zero-carbon practices, GAC Honda Development Zone's new energy factory has improved energy efficiency in terms of raw materials, production processes, environmental protection management, energy conservation and carbon reduction; and on December 19, 2024, it obtained the carbon neutrality declaration certificate issued by the Guangzhou Carbon Emissions Trading Center.
With P7 as the link and relying on 26 years of quality accumulation, GAC Honda is using digital and technological innovation as a breakthrough to continue to impress new and old users.